On behalf of BASF, Geocom realized the NaviLu project by developing an offline turn-by-turn navigation app based on the ArcGIS Runtime SDK to optimize plant logistics and visitor traffic. The app enables employees, visitors and truck drivers to safely reach their destination at the plant using the optimal route, taking into account the daily road closures. By integrating the application with the central logistics system, the user interaction between driver and app is minimized. The centrally maintained road closures are automatically transferred to the users when changes are made.
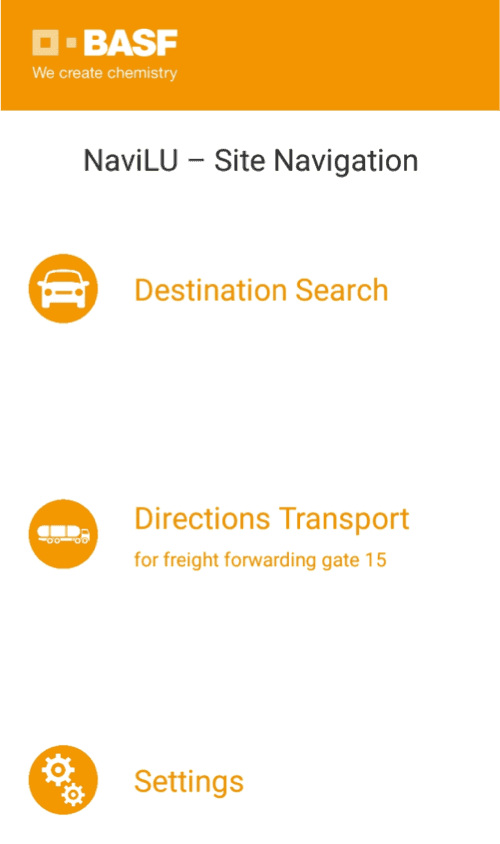
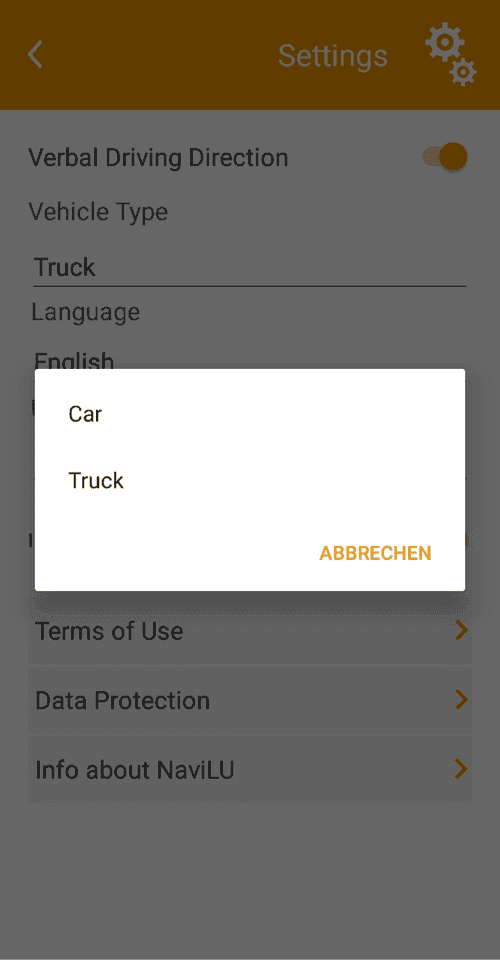
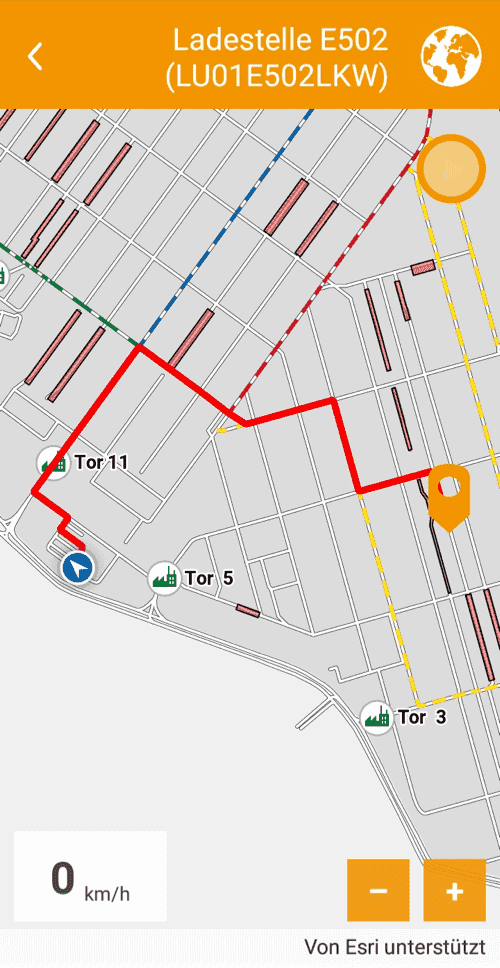
Key features
Cross-platform solution
Built with the ArcGIS Runtime SDK for .NET and Xamarin Forms so the app can be deployed to Android and iOS.
Offline maps to power disconnected, turn-by-turn navigation
Maps of the industrial site were created with ArcGIS Pro and made available to the app as an MMPK for display and routing.
Sync with a feature service
When a connection is available, download and sync barriers, such as road closures, from a feature service.
App details
With an area of around ten square kilometers, BASF's site in Ludwigshafen am Rhein (Germany) is the world's largest chemical site. It is characterized by very complex infrastructure consisting of approximately 200 production facilities, 2,000 buildings, 230 km of railway tracks and 106 km of roads. In addition to the 39,000 employees, several thousand visitors and external service providers enter the site every day.
Large and complex plant sites such as the BASF SE plant in Ludwigshafen differ from public road infrastructures in terms of structure, appearance and traffic management. BASF SE strives to actively control traffic at the site in order to reduce the time external trucks spend on the site with the aim of using the existing traffic infrastructure most effectively and minimizing the risk of accidents.
On behalf of BASF, Geocom realized the NaviLu project by developing an offline turn-by-turn navigation app based on the ArcGIS Runtime SDK to optimize plant logistics and visitor traffic. The app enables employees, visitors and truck drivers to safely reach their destination at the plant using the optimal route, taking into account the daily road closures. By integrating the application with the central logistics system, the user interaction between driver and app is minimized. The centrally maintained road closures are automatically transferred to the users when changes are made.
In order to guide trucks from the gate to the loading point, plant maps with detailed information on logistics-relevant infrastructure objects such as gates, scales, loading points and parking spaces are required. Standard navigation systems usually do not contain such features. In addition, the calculation of the optimal route on the plant has to consider the instructions of the factory traffic department and must always take into account the latest road closures.
Using the routing technology, routes can be calculated even offline on a smartphone, adapting the business processes and the conditions of a plant location. In contrast to competing solutions, this architecture allows an efficient, integrated and fully automated process of card and data management by the customer.
The app for offline turn-by-turn navigation was developed on the basis of the ArcGIS Runtime SDK for .NET as a cross-platform solution and made available for the iOS and Android platforms. ArcGIS Enterprise is used to share information between the central order system for logistics, space management, and the app.
Learn more
- Build cross-platform apps with ArcGIS Runtime SDK for .NET and Xamarin Forms
- Transportation